直线滚珠丝杆在精密传动设备(如数控机床、自动化机械、伺服滑台等)中承担着高精度直线运动的核心功能,卡顿现象会直接影响设备的定位精度、运行稳定性,甚至缩短使用寿命。解决卡顿问题需结合其结构原理(由丝杆、螺母、滚珠、循环装置组成,通过滚珠滚动实现低摩擦传动),从机械配合、润滑状态、负载条件、安装调试等多方面排查,具体解决方法如下:
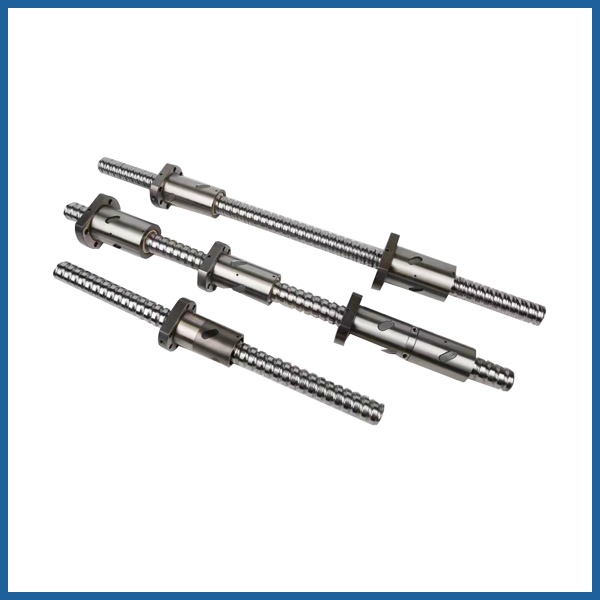
一、排查机械结构与配合问题
滚珠丝杆的卡顿多源于机械部件的异常接触或卡滞,需优先检查以下部位:
丝杆与螺母的配合间隙异常
问题表现:长期使用后,滚珠磨损、循环装置(如返向器、端盖)变形,导致滚珠在滚道内卡涩;或装配时螺母与丝杆轴线偏移,产生附加力矩,阻碍滚动。
解决方法:
拆解螺母,检查滚珠是否磨损、破裂或数量缺失(需补充同规格滚珠,通常为高碳铬轴承钢材质);
检查循环装置(返向器)是否松动、变形或磨损,若有则更换对应配件(注意型号匹配,如内循环 / 外循环结构不同);
用百分表检测丝杆与螺母的同轴度,若偏移超差(通常要求≤0.1mm/m),需重新校准安装基准(如调整导轨平行度、紧固螺母座)。
丝杆弯曲或直线度超差
问题表现:丝杆受外力撞击、长期重载或存放不当导致弯曲,旋转时与螺母内壁产生局部摩擦,出现周期性卡顿(尤其在特定行程位置)。
解决方法:
用大理石平台或激光干涉仪检测丝杆直线度,若误差超过 0.02mm/m(精密级),需进行校直处理(小型丝杆可手动压力校直,大型丝杆需专业设备);
严重弯曲时直接更换丝杆(避免强行使用导致螺母进一步磨损)。
支撑轴承故障
问题表现:丝杆两端的支撑轴承(如角接触球轴承)磨损、游隙过大或卡涩,会导致丝杆旋转时产生径向跳动,传递至螺母引发卡顿。
解决方法:
拆卸轴承座,检查轴承是否有异响、滚珠磨损或保持架断裂,若有则更换同型号轴承(注意预紧力调整,避免过松或过紧);
重新装配轴承时涂抹高温润滑脂(如锂基脂),确保旋转顺滑。
异物侵入滚道
问题表现:粉尘、铁屑、冷却液等杂质进入丝杆与螺母的滚道,导致滚珠滚动受阻,出现突发性卡顿(伴随异响)。
解决方法:
用高压气枪清理滚道内可见杂质,再用煤油或专用清洗剂冲洗(拆卸螺母后冲洗更彻底);
检查防护装置(如伸缩护罩、波纹管)是否破损,破损需及时更换,防止后续异物侵入。
二、优化润滑状态
滚珠丝杆依赖润滑脂 / 油减少滚珠与滚道的摩擦,润滑不良是卡顿的常见原因:
润滑脂干涸或选型错误
问题表现:长期未补脂导致润滑脂干涸,或使用了黏度不符的润滑脂(如低温环境用了高温脂,导致流动性差),会增加滚动阻力。
解决方法:
清理旧润滑脂,根据工况选择合适型号(如高速场合用低黏度锂基脂,重载场合用极压脂,食品行业用食品级润滑脂);
按说明书要求定期补脂(通常每运行 100 小时或每月一次),注脂量以填满滚道 1/3-1/2 为宜(过多易产生阻力)。
油路堵塞
问题表现:自动润滑系统的油管堵塞、注脂嘴被杂质堵住,导致润滑脂无法进入滚道。
解决方法:
检查润滑系统管路,疏通堵塞部位;若注脂嘴损坏,更换同规格嘴头;
手动注脂时确保油脂均匀分布(可旋转丝杆帮助油脂扩散)。
三、调整负载与运行参数
过载或运行参数不合理会导致丝杆受力异常,引发卡顿:
负载超过额定值
问题表现:轴向负载过大(超过丝杆额定动载荷)、径向负载超标(丝杆不承受径向力,若有会导致偏磨),均会使滚珠与滚道接触应力过大,出现卡滞。
解决方法:
核算实际负载(包括工件重量、惯性力),若超过额定值,需更换更大规格的丝杆(如增大直径、提高导程);
检查是否存在额外径向力(如导轨平行度差导致的侧向力),通过调整导轨安装精度消除径向负载。
运行速度与加速度设置不当
问题表现:启动 / 停止加速度过大,导致丝杆瞬间受力冲击,滚珠在滚道内打滑或卡滞;高速运行时因离心力过大,润滑脂流失过快,加剧摩擦。
解决方法:
在控制系统中降低加速度(如从 500mm/s² 降至 300mm/s²),使运动更平稳;
检查丝杆最高转速是否超过临界转速,若超上限需缩短支撑间距或降低转速。
四、检查安装与固定部件
安装精度不足会导致丝杆运行时受力不均,引发卡顿:
螺母座与工作台固定松动
问题表现:螺母座螺栓松动,导致螺母在运动中与工作台相对位移,产生额外摩擦力。
解决方法:
用扭矩扳手按规定力矩重新紧固螺母座螺栓(如 M8 螺栓通常用 25-30N・m);
加装防松垫片(如弹簧垫片、齿形垫片),防止振动导致再次松动。
丝杆支撑座定位误差
问题表现:两端支撑座轴线不共线,或与导轨不平行,导致丝杆受附加力矩,运行时出现周期性卡顿。
解决方法:
用百分表校正支撑座的同轴度(误差≤0.05mm),调整垫片厚度使轴线对齐;
以导轨为基准,用激光干涉仪检测丝杆与导轨的平行度(误差≤0.02mm/m),通过研磨支撑座底面进行调整。
五、长期使用后的维护与更换
若丝杆已严重磨损(如滚道剥落、滚珠变形),单纯维修无法解决问题:
判断磨损程度:用手转动丝杆,若手感明显顿挫、异响持续,或测量定位精度超差(如重复定位误差>0.01mm),说明磨损严重。
更换原则:优先更换整套丝杆螺母副(确保匹配精度),并同步更换支撑轴承和润滑系统配件;更换后需重新校准定位精度和运行参数。